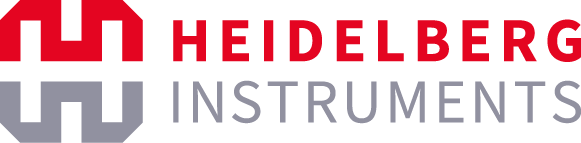
μMLA
MLA150
MLA300
桌上型無光罩曝光機
無光罩雷射直寫曝光機
專業自動化雷射直寫曝光機
CONFIGURABLE AND COMPACT TABLETOP MASKLESS ALIGNER WITH RASTER SCAN AND VECTOR EXPOSURE MODULES
可根據需求進行配置
具有光柵掃描和向量曝光模組
THE FASTEST MASKLESS ALIGNER FOR R&D, RAPID PROTOTYPING AND SMALL PRODUCTION VOLUMES, DESIGNED FOR BINARY LITHOGRAPHY
最快速無掩模對準器用於研發、快速原型製作和小批量生產,專為二次微影而設計
OPTIMIZED FOR INDUSTRIAL MANUFACTURING, ENSURING HIGH THROUGHPUT AND SEAMLESS PRODUCTION LINE INTEGRATION
優化工業製造,確保高通量並實現生產線自動化整合
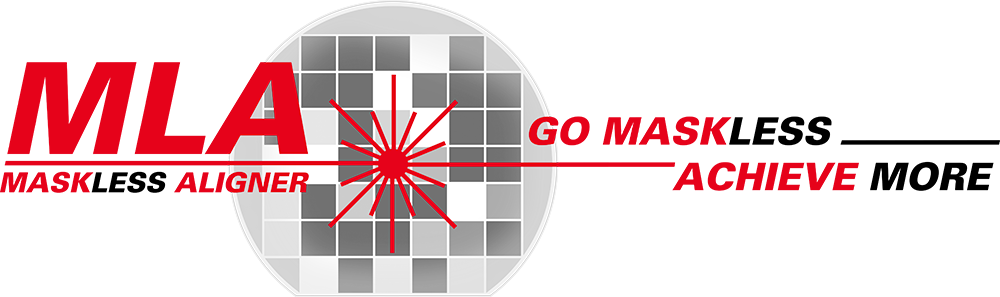
µMLA 是一款靈活且可依需求配置的工具,提供兩種曝光模式。標準的 µMLA 使用光柵掃描模式進行曝光,該模式速度快,可提供卓越的圖形品質和精度,且寫入時間與圖形結構尺寸無關。可選配的向量掃描模式,則可以更快速、更準確的對連續平滑曲線圖形 (例如波導) 進行製作。三種光學寫頭提供了高分辨率和吞吐量的選配,使用者可以依需求選擇不同的分辨率和速度,針對特殊應用優化曝光效果。繪制模式 (Draw Mode) 允許對現有結構進行簡單的即時修改,包括用於奈米線及 2D 材料的調整。且提供灰度曝光模式可以創建複雜的 2.5D 結構,例如微光學元件。µMLA 擁有小巧的體積可以輕鬆擺放在桌面,是一款完美的入門研發 (R&D) 工具。
The µMLA is a flexible and customizable tool, and offers two exposure modes. The standard µMLA uses the Raster Scan Exposure Mode for exposures, which is fast and provides excellent image quality and fidelity, while the write time is independent of structure size of pattern density. The optional Vector Scan Mode is designed for patterning continuous smooth curves such as waveguides in a faster and more accurate way. Three optical setups offer a choice of variable resolution and throughput. Each allows easy switching between different resolution and speed configurations to optimize exposure for a given application. The Draw Mode enables straightforward ad-hoc modifications to existing structures and electrical contacts to nanowires or 2D materials. The grayscale exposure mode allows the creation of complex 2.5 structures such as micro-optical devices. With its small footprint, the µMLA fits on a regular table.
MLA 150 是最先進的無光罩雷射直寫工具。
應用領域包括量子器件 (2D 材料、半導體材料、奈米線等) MEMS、微光學元件、感測器、執行器、MOEMS 等材料及生物醫學元件。
我們的無光罩曝光機於 2015 年首次推出,現在已成為傳統光罩機的替代品,完全屏除對光罩的需求;
無光罩镭射直写解決方案明顯縮短製作時間,只需更改 CAD 佈局即可快速修改任何設計。 MLA150 還具有快速自動化的正面和背面對準程序以及傑出的速度:曝光 100 x 100 mm² 的區域且小至 1 µm 的結構不用 10 分鐘實現作品。
MLA 150 成功故事
2022 年安裝第 150 台 MLA 150
The Maskless Aligner MLA 150 is a state-of-the-art Maskless Lithography tool.
Areas of application include nanofabrication of quantum devices (2D materials, semiconductor materials, nanowires, etc.) MEMS, micro-optical elements, sensors, actuators, MOEMS and other devices for materials and life sciences.
Our Maskless Aligner series, first introduced in 2015, is now firmly established as an alternative to the traditional mask aligner, fully eliminating the need for masks.
The maskless approach leads to significantly reduced cycle times.
Any design modifications can be quickly implemented by simply changing the CAD layout.
The system also features fast automated front- and backside alignment procedures and outstanding speed: Exposing an area of 100 x 100 mm² with structures as small as 1 µm takes less than 10 minutes.
The 150th MLA 150 installed in 2022:
The MLA 150 Success Story
MLA 300 實現最高的光學品質和精度,標準曝光模組能夠實現最小 1.5 µm 特徵尺寸。
在我們的計畫將會達到更高通量及更高分辨率的寫入模式。
MLA 300 配備全自動化功能,支援可定致的裝載選項,適用於生產環境的軟體設計並採用專利的基材追蹤技術。
MLA 300 通過屏除光罩採購、驗證和管理的需求,因此降低了生產成本和工作量。
由於搭載長效的曝光雷射器 (estimated 10 years at 24/7 production) ,減少消耗使得操作成本大幅降低。
即時自動對焦功能可補償基材的翹曲或波紋,確保圖案精準度。
無光罩微影技術支援對每個晶片進行圖案校正和序列化,能夠完整追蹤產品特性,例如感測器校準。
The MLA 300 achieves the highest optical quality and precision.
The standard exposure module achieves a minimum feature size of 1.5 µm.
Writing modes for higher throughput and higher resolution are on our roadmap.
The MLA 300 features full automation with customizable loading options, software designed for production environments, and patented substrate tracking technology.
The MLA 300 reduces production costs and effort by overcoming the requirement for mask procurement, verification, and management.
Operating costs benefit from a long-lifetime exposure laser (estimated 10 years at 24/7 production) and fewer consumables.
Modularity enables fast maintenance, replacement, or repair. Real-time autofocus compensates for substrate warp or corrugations, ensuring flawless patterning.
Maskless Lithography allows per-die pattern corrections and serialization for full tracing of product characteristics, such as sensor calibration.

KEY FEATURES
Substrate size: from 5 mm to 5” Minimum feature size: down to 0.6 µm Maximum write speed (at 4 µm resolution): 200 mm2/min Real-time autofocus system Frontside alignment Easy-to-use operating software 2 available optical setups Choice of exposure Module: Raster and/or Vector scan Variable resolution Draw Mode Wavelengths (Raster Scan): 390 nm or 365 nm exposure wavelength Wavelengths (Vector Scan): 405 nm and/or 375 nm Overview camera for alignment and inspection
Minimum substrate size: 3 mm x 3 mm Maximum exposure area: 6” x 6” (optional 8”x 8”) Minimum structure size down to 0.6 μm Maximum write speed: 1400 mm2/min at 1 μm feature size Real-time autofocus Overview camera for fast alignment and inspection Front- and backside alignment Temperature-controlled environmental chamber Exposure wavelengths: 405 nm and / or 375 nm Draw Mode for CAD-less exposure Standard Grayscale Exposure Mode High-Aspect Ratio Mode Easy-to-use operating software
Maximum exposure area: 300 mm x 300 mm Minimum feature size: 1.5 μm Minimum lines and spaces: 2 µm Maximum write speed: 5000 mm2/min (at 405 nm, with one module) Real-time autofocus Overview camera for fast alignment and inspection Front- and backside alignment Temperature-controlled environmental chamber Exposure wavelengths: 405 nm and / or 375 nm

Application
MEMS Micro-Optics Semiconductor Sensors Actuators MOEMS Material Research Nano-Tubes Graphene
MEMS Micro-Optics Semiconductor Sensors Actuators MOEMS Material Research Nano-Tubes Graphene
MEMS Micro-Optics Semiconductor Sensors Actuators MOEMS Material Research Nano-Tubes Graphene
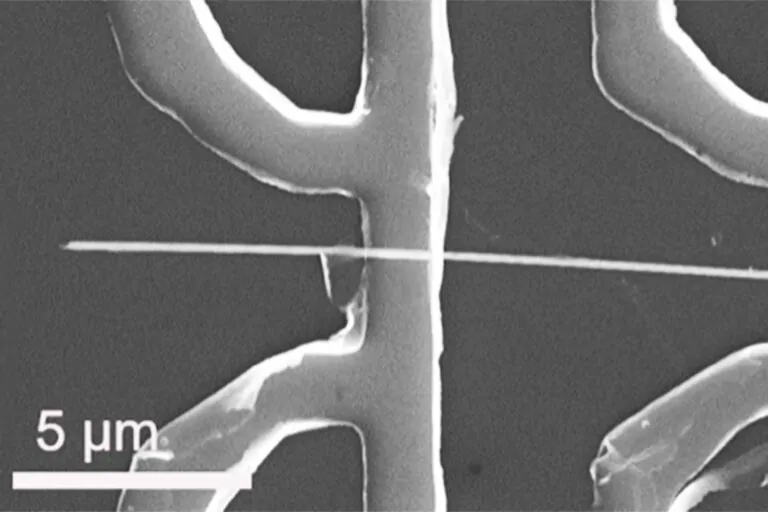
Single Ni nanowires (horizontal line in the image) with two precisely aligned thermometer structures used to investigate Co-Ni alloy magneto-thermopower and magneto-resistance. (Courtesy of Tim Boehnert, University of Hamburg)
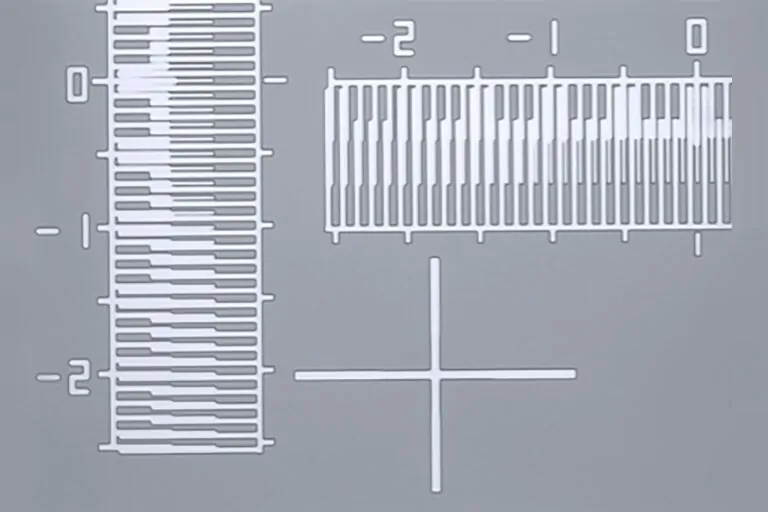
In many applications, several layers need to be exposed on the same substrate. The cameras of the μMLA can automatically detect alignment markers and adjust the position, rotation, scaling and orthogonality of the exposure to the existing structures. The image shows vernier scales and a “cross-in-cross” structure, employed to measure the remaining offset in x and y direction.
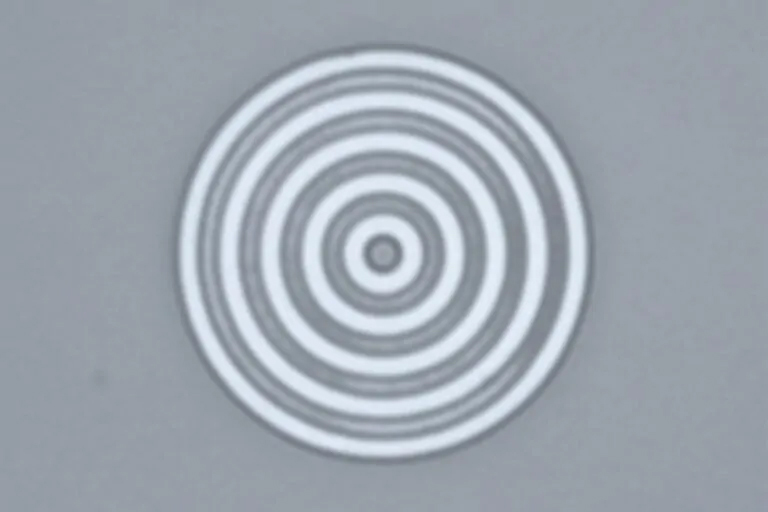
Concentric rings with 1 μm line width were written into the photoresist using the Raster Scan Exposure Mode.
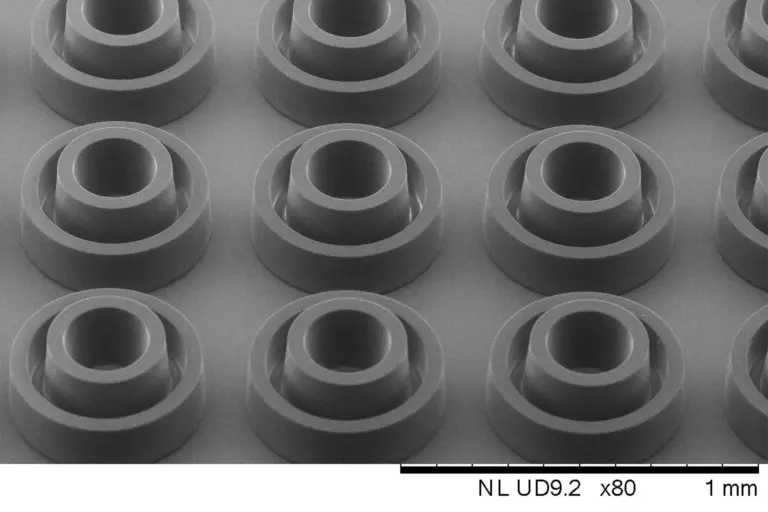
Dual-compartment microcontainers for combination therapy, to achieve a physical separation of two drugs followed by a sequential release. The corresponding paper is linked in our library (DTU Kopenhagen: Christfort, J. F., et al. Adv. Therap. 2022, 5, 2200106)
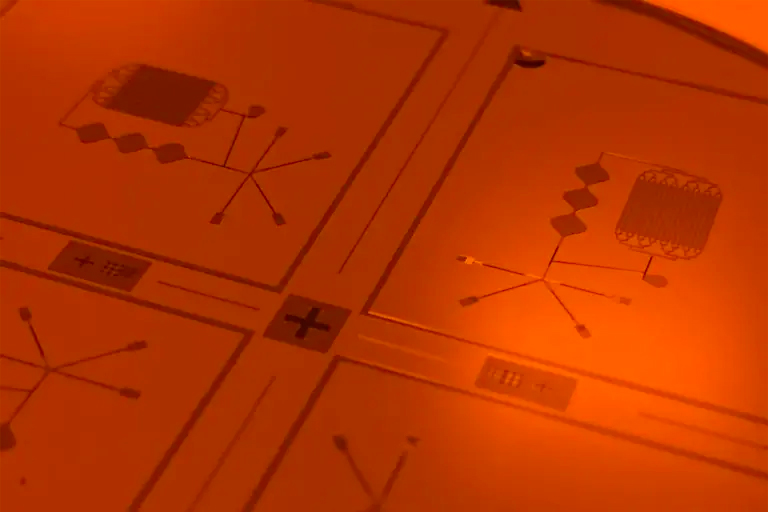
Micro fluidic structures made in two layers of materials: 1. AZ10XT (14 µm, thermally cross-linked by customer) and 2. SU-8 (20µm, aligned to first layer) (Courtesy of Max-Planck-Institute for terrestrial microbiology)
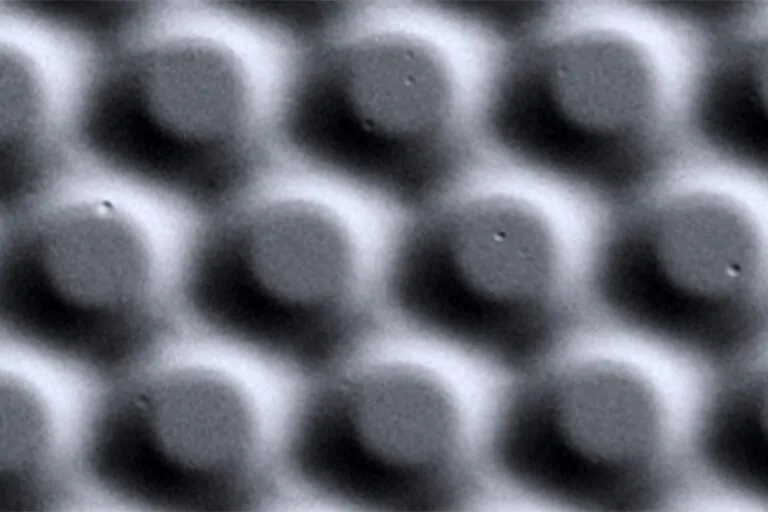
The μMLA also offers a standard Grayscale mode, which allows the creation of structures for a wide range of applications in micro-optics. This example shows micro-lenses written in 15 μm thick AZ4562, with a pitch of 30 μm and a radius of curvature of 16 μm.
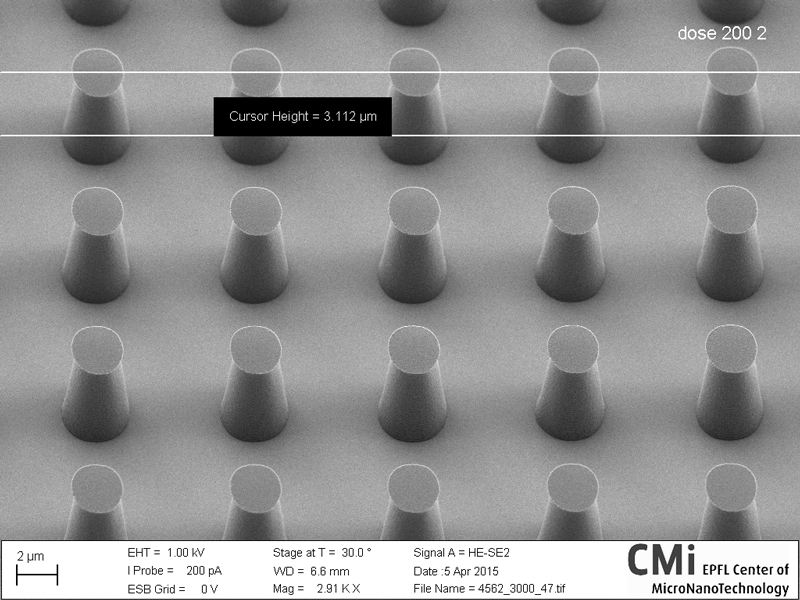
A gear wheel patterned in 800 µm thick SU-8 demonstrates the capability of the MLA 150 to create vertical sidewalls in thick forks, gear wheels, piezoelectric material, bio-, chemical or pressure sensors, or other miniaturized physical devices.
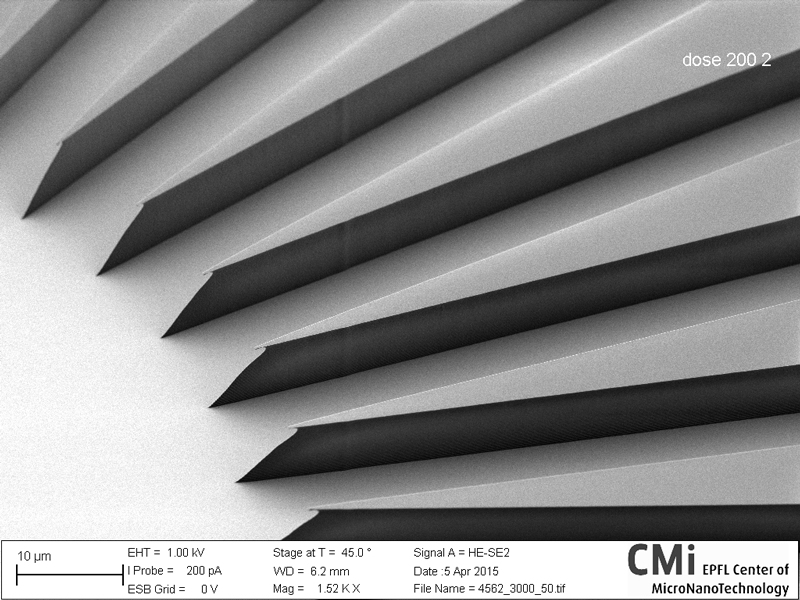
A master for a microfluidic mixer to be transferred by soft lithography in PDMS. The structure is patterned in 100 μm SU-8 with the 375 nm laser wavelength of the MLA 150. This type of structure requires high-throughput for fast large-area patterning and precise stitching to ensure channel smoothness. (Courtesy of CMi EPFL Center of MicroNanoTechnology)
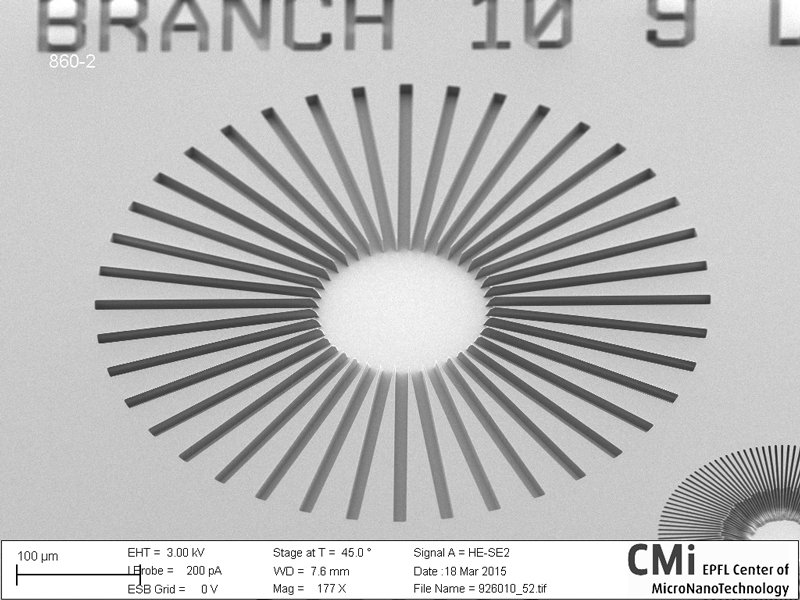
Nanoholes as precisely positioned traps for nanoparticles fabricated using “mix-and-match” lithography. The 100 nm square “nanoholes” patterned with e-beam lithography are separated by the coarse trenches created using the MLA 150, which are precisely aligned to the existing nanohole pattern. (Courtesy of EPFL LMIS1, Lausanne)
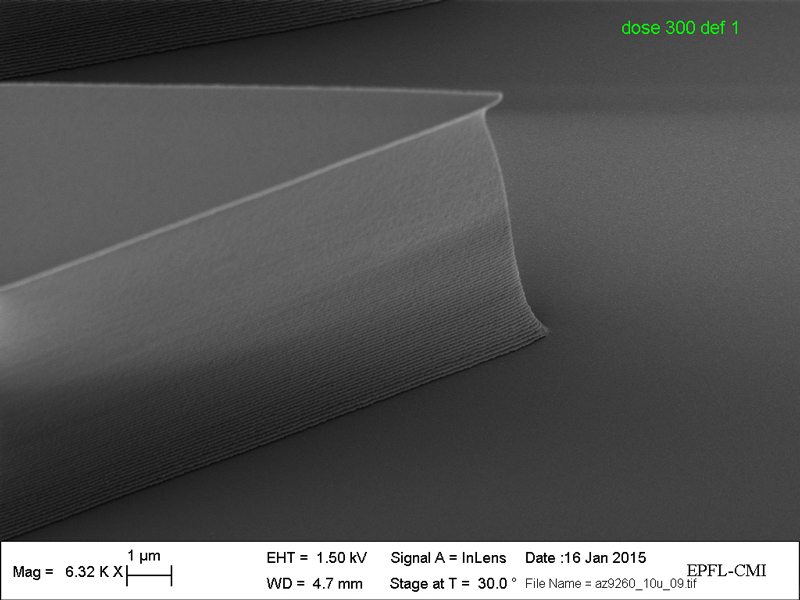
An array of SQUIDs (superconducting quantum interference device) used for the readout of metallic magnetic microcalorimeters (high-resolution particle detectors operated at low temperatures). These devices are microfabricated in large arrays and comprise up to 18 layers with submicron features. The MLA 150 ensures the extreme overlay accuracy crucial for this application. (Courtesy of the Kirchhoff Institute for Physics (KIP), Heidelberg University)
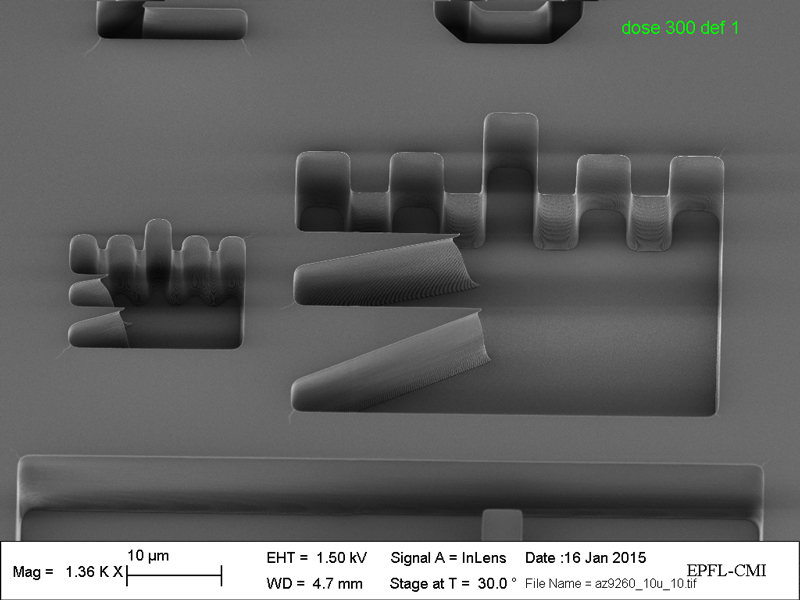
This specific patterning of “OSTEmers” retinal implants shows an example of novel medical implants. Bio-compatible, impermeable, and UV-curable OSTEmers are highly promising for artificial retina. Contactless exposure with the MLA 150 enables the patterning of this material, which is a viscous liquid during processing, and is virtually impossible to work with using other lithography tools. (Courtesy of EPFL, Neuroengineering Laboratory)
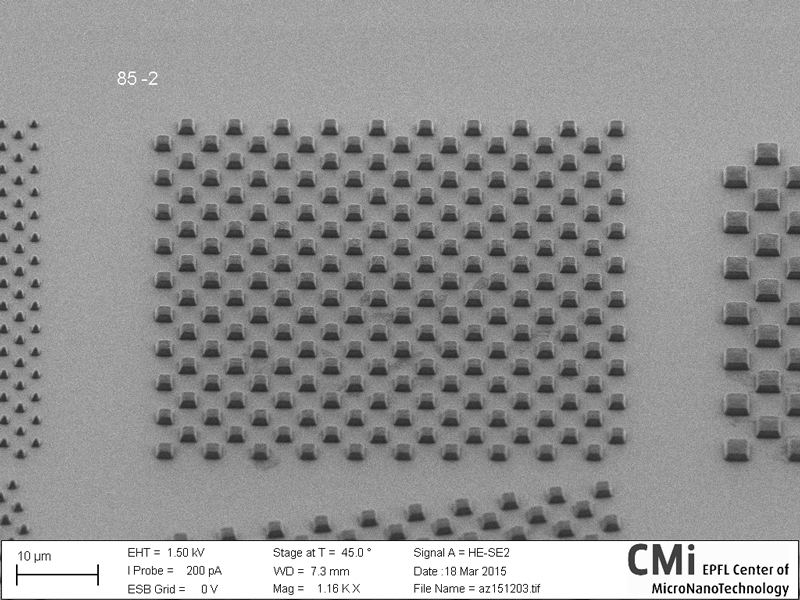
A wafer of superconducting detectors for the South Pole Telescope (SPT) camera. The camera carries an array of over 16000 such devices. Each of them comprises ultra-thin superconducting elements with features as small as 1 μm. Here, the MLA 150 was used to fabricate the Nb leads, which appear as bands in between the pixels. (Courtesy of CNM at Argonne National Laboratory, photo by Clarence Chang)
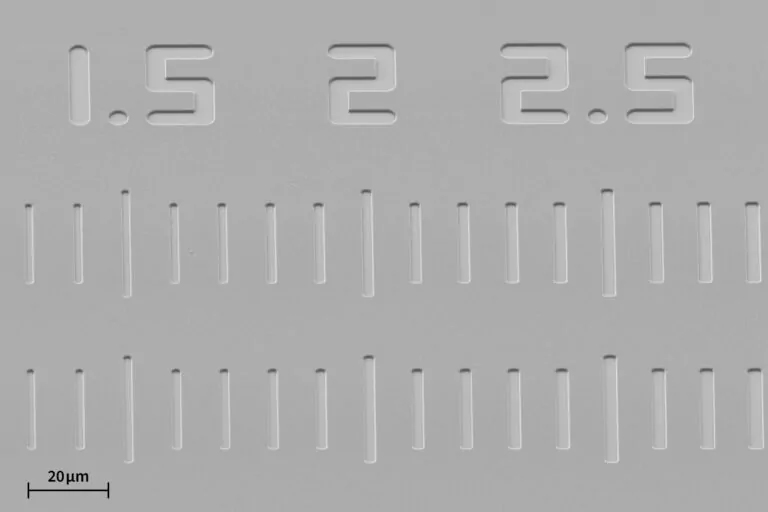
Resolution pattern exposed in a 500 nm layer of AZ1500 showing a minimum feature size of 1.5 µm. (SEM image, viewed with a 45° angle)
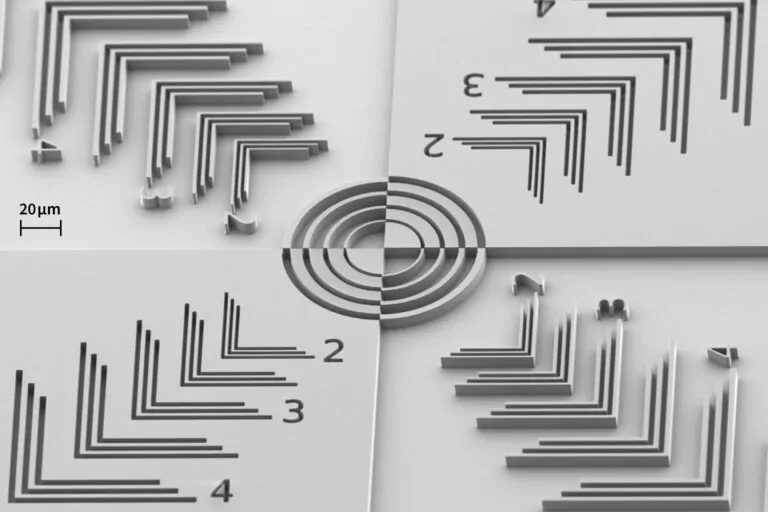
Test structures exposed in a 10 µm layer of AZ 10XT. (SEM image, viewed with a 45° angle)
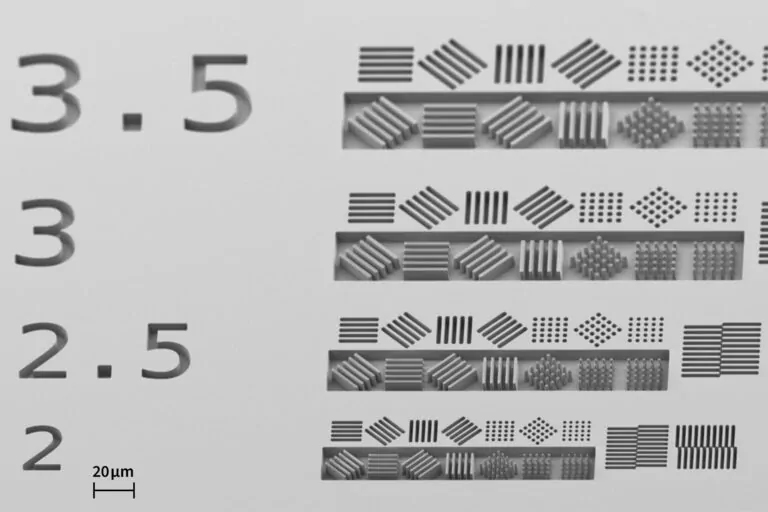
Resolution pattern exposed in a 10 µm layer of AZ 10XT showing an aspect ratio of 1:5. (SEM image, viewed with a 45° angle)
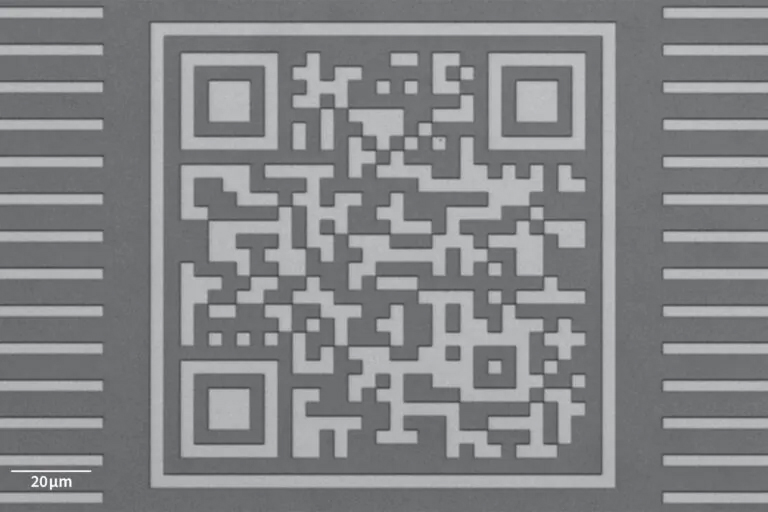
Optical microscope view of a micro QR code exposed in AZ1500 (500 nm) resist.
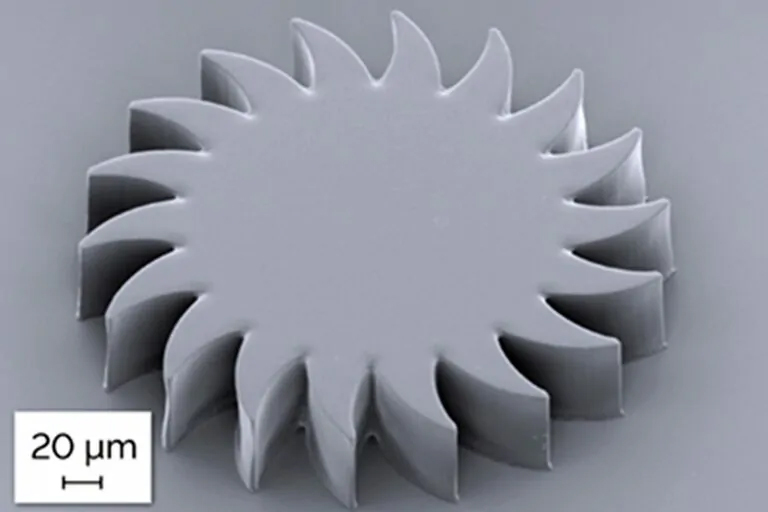
MEMS processes integrate standard microchip technologies with electromechanical components of a diverse range of sizes and materials. Stresses and stress-induced deformations need to be managed carefully to yield correct device properties. The Maskless Aligner technology is ideally suited to make on the fly corrections to the design, if required.
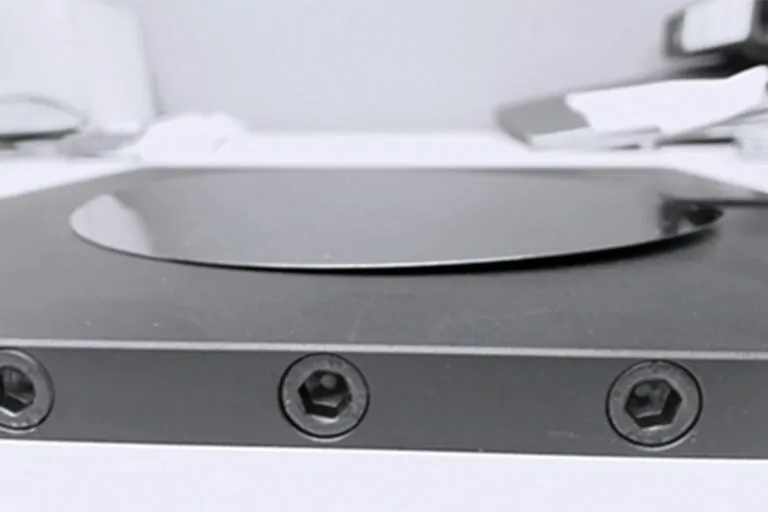
Structuring flexible substrates is challenging as the shape and the distortions vary with applied forces. Maskless lithography offers the unique option of exposing the substrates with warpage-dependent pre-distortions, to maximize yield.
Reach Us
想要知道更多資訊嗎? 沒問題,快與我們聯繫!
© Stella Technology Co., Ltd.